Over the last 15 years, there have been significant developments in new devices for energy recovery, new membrane materials and new sizes and orientations of reverse osmosis (RO) plants, all designed to reduce costs and improve efficiency. The fundamental issue of keeping membrane surfaces clean to ensure efficient RO plant operation has seen relatively few recent developments. This is surprising as any fouling of the membrane surface will have a dramatic effect on energy consumption and plant efficiency. Many researchers have focused on identifying and studying the foulants in great detail, but there have been few studies in how to remove it. Commodity acid and alkali compounds are still widely used due to the perceived lower application costs. Specially blended cleaning chemicals incorporating detergents, surfactants and chelants are also in wide use and are increasingly accepted by the market to be economically and environmentally viable. “Strategically pairing chemical agents that have complementary cleaning mechanisms so a higher cleaning efficiency can be attained” has been described.
We have established a research project to explore in detail the use of novel physical and chemical cleaning methods. These included normal chemicals, physically generated two layers micro bubbles that designed to agitate the cake layer on the membrane surface, assisting deposit removal.
A series of experiments pilot plant have been completed. The presence of two layer micro bubbles has a dramatic effect on cleaning efficiency as a result of agitation of deposits on the membrane surface. These improvements occurred because cleaning using two layer micro bubbles has been more effective and the membrane surface much cleaner than previously. A clean membrane surface does not foul as quickly as a dirty membrane surface due to surface roughness.
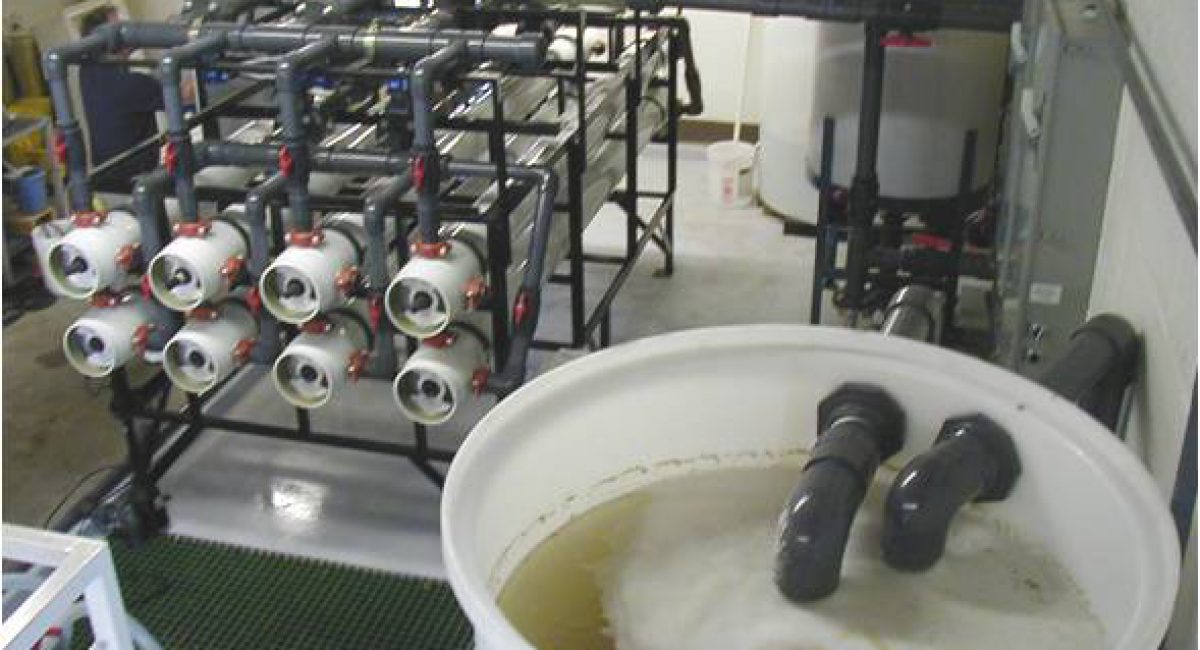
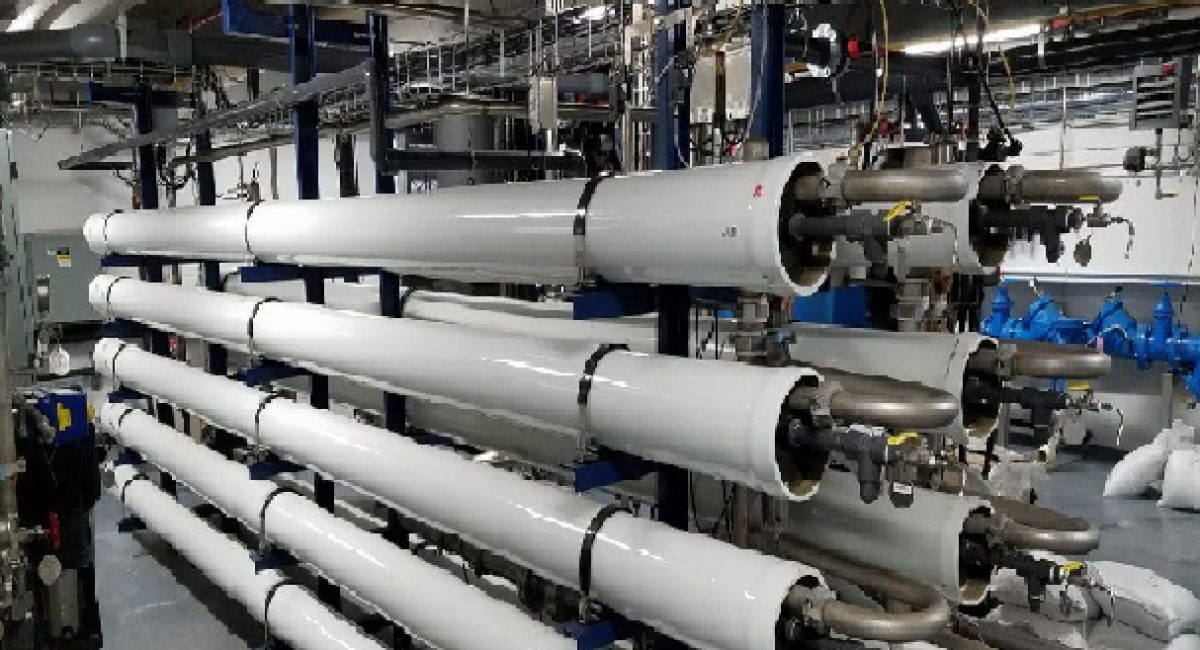
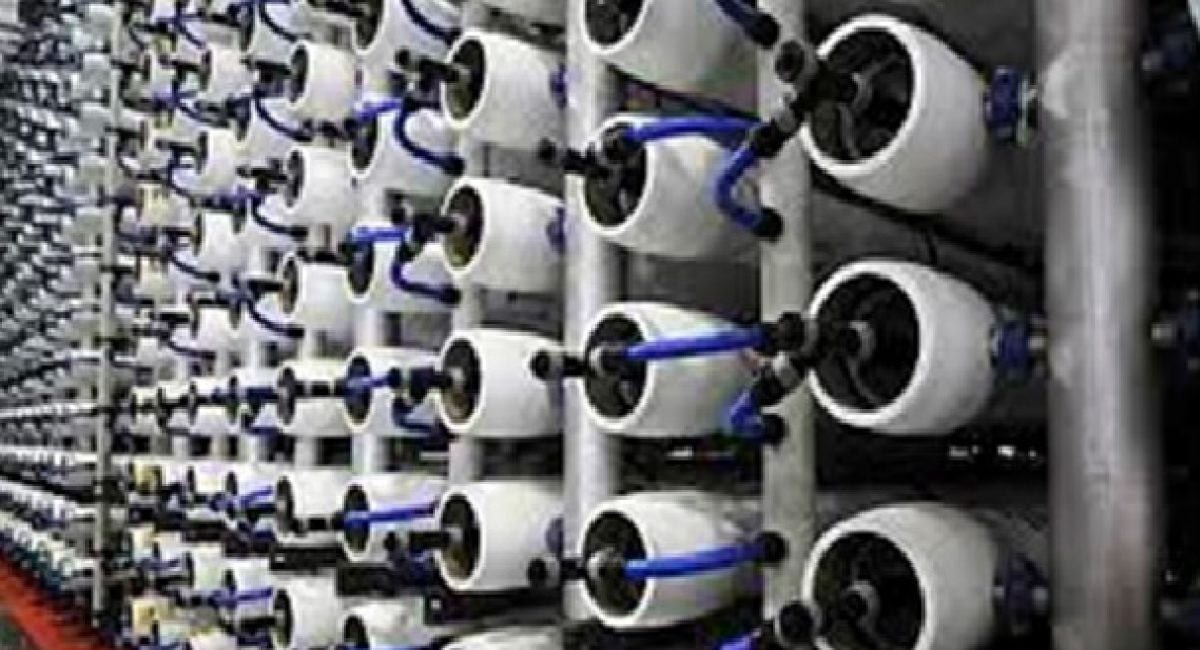